孟凡生1,2,陰秀麗1,蔡建渝1,馬隆龍1,吳創之1
(1.中國科學院廣州能源研究所,中國科學院可再生能源與天然氣水合物重點實驗室,廣州510640;2.中國科學院研究生院,北京100049)
摘要:生物質氣化氣的組分對內燃機的排氣溫度、最大爆發壓力、有效熱效率和尾氣排放都具有重要影響。各種氣體成分的燃燒速率以及其中的阻燃成分都直接影響氣缸內混合氣的燃燒,同時影響內燃機的尾氣排放。分析發現內燃機的排氣溫度過高、爆發壓力偏低、能耗偏高的主要原因是由于生物質氣化氣熱值低、燃燒速度慢;通過對尾氣排放的測試分析發現,混合氣的完全燃燒可以降低碳煙、CO和HC的排放,降低燃燒溫度可以降低NOx的生成率。
0引言
生物質是一種可再生能源,由于其生長和利用過程構成自然界碳循環,其高效利用可有效減少溫室氣體的排放。傳統的生物質能利用是采用直接燃燒方式,不僅效率低下,而且會排放出大量煙塵和余灰,污染環境;生物質氣化技術是通過熱化學反應,將固態生物質在不完全燃燒條件下,使較高分子量的有機碳氫化合物鏈裂解,變為較低分子量的H2、CH4、CO等可燃氣體[1]。氣化獲得的氣體燃料作為一種清潔能源,適用范圍廣,同時提高了生物質利用的能源品位和利用效率,應用前景廣闊。氣化發電過程包括3個方面:生物質氣化;氣體凈化;燃氣發電[2,3]。燃氣內燃機與蒸汽輪機、燃氣輪機相比具有機組容量范圍大,燃氣熱值應用范圍廣的優勢,進而使得利用燃氣內燃機發電在中國的分布式發電領域得到廣泛應用。目前國內所應用的生物質燃氣內燃機大部分是由中低轉速柴油機改裝的,功率大都低于400kW。
任永志等[4]對意大利Tessari的80kW燃氣發電機與生物質氣化氣的匹配性作了分析。中國科學院廣州能源研究所在國家高技術發展計劃(863計劃)支持下,開展了5MW生物質氣化-蒸汽聯合循環發電示范工程研究,系統中采用了600kW燃氣內燃機8300(600r/min)進行發電。本文分析了該系統中內燃機的排溫、動力和排放性能。
1生物質氣化氣特性分析
生物質氣化采用循環流化床空氣氣化,原料為稻殼。主要流程如圖1所示,氣化爐出來的氣體流經旋風分離器、焦油裂解爐、高溫過熱器、文丘里除塵器、噴淋塔、羅茨風機到達儲氣罐,儲氣罐內的氣體流經進氣管道進入內燃機燃燒做功,內燃機曲軸飛輪端帶動發電機進行發電,高溫過熱器出來的氣體與內燃機排放的尾氣進入加熱鍋爐,鍋爐出來的高溫水蒸氣帶動蒸汽輪機發電[5]。
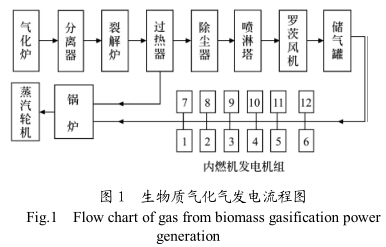
對于燃燒生物質氣化氣的燃氣內燃機首先要求使用的氣體燃料能在點燃條件下進行正常的點火燃燒,并且要求燃料燃燒完全,能夠穩定燃燒,以保證發動機充分發揮其動力性能和經濟性能;燃料應具有較高的熱值,以保證發動機有較高的效率;還要保證燃料潔凈性的要求,以減少氣缸腐蝕和零部件的磨損。
氣化當量比(單位質量生物質在氣化過程中所消耗的空氣量與生物質完全燃燒所需要的理論空氣量之比)在0.22-0.35之間變化時,在羅茨風機出口取樣19次,檢測出H2、CH4、CO2、CO、O2、N2、C2H2、C2H4、C2H6氣體組分的含量,其體積百分含量如表1所示,對于生物質氣化氣組分分析如下:
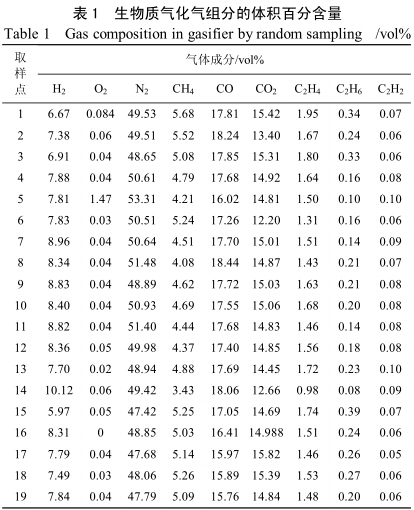
1.1氣體組分分析
測得的9種氣體中H2、CH4、CO為主要可燃組分,CO2、N2為阻燃成分。
CH4是天然氣的主要成分,辛烷值高達130[6],因而具有良好的抗爆性,然而火焰傳播速度小,燃燒速度慢;CO為最為主要的可燃氣體成分,但燃點較高;H2相對于其他可燃氣體而言,具有火焰傳播速度快、易擴散以及傳熱能力強的特點,并且火焰傳播速度隨氧濃度的增加而提高[7]。生物質氣化氣中H2的變化范圍較大,在6%~10%間波動。H2與空氣混合的最大燃燒速度為2.80m/s[8],當氫氣含量較高,過量空氣系數較小時,缸內混合氣的燃燒溫度高,壓力升高率大,將會導致部分未燃混合氣的著火誘導期縮短,極易引***燃;點燃氫氣所需要的點火能量僅為0.02MJ,不足汽油的1/10,這就意味著氣缸內的局部溫度高的點可以成為著火點,引起早燃[9]。
氣化氣中有近一半的N2,CO2含量也在15%左右,而且對于三原子分子的CO2具有的摩爾比熱遠大于空氣,因而在內燃機壓縮和燃燒沖程中會大量地吸收熱量,使發動機壓縮終點的溫度降低,導致點火推遲,燃燒溫度降低;阻燃成分的存在會減緩焰前反應,阻礙燃燒的正常進行,對火焰的燃燒速度起到負面的影響,致使內燃機后燃嚴重,排氣溫度較高。
1.2熱值分析
通過計算,生物質氣化氣熱值在5.30-6.43MJ/Nm3之間,相對于天然氣熱值為35.91MJ/Nm3[8](按照純CH4計算)而言,屬于低熱值氣體。
由于在內燃機氣缸中燃燒的是燃氣和空氣組成的混合氣,因而在實際循環中應考慮混合氣的熱值。
天然氣完全燃燒時的化學反應式為:
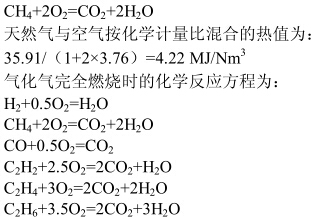
生物質氣化氣與空氣按化學計量比混合的熱值在2.49~2.67MJ/Nm3之間。因而無論氣化氣的熱值還是理論混合氣熱值與天然氣相比,都存在較大差距,使得同一規格的內燃機,在燃燒生物質氣化氣時出力明顯不足[10]。
1.3氣體中雜質的影響
雖然生物質燃氣經過了嚴格的凈化,但仍含有大量的焦油和灰分,測得羅茨風機出口的焦油含量接近100mg/m3[11]。工作中內燃機的高溫工作環境使得生物質氣化氣成分中的焦油,以及一些細灰顆粒在燃燒過程中引起氣門處積炭,導致氣門關閉不嚴,使得氣門漏氣,氣缸內高溫高壓氣體沖刷氣門彈簧,促使彈簧受熱退火、彈性減弱,進而影響整個配氣機構的工作;在內燃機工作過程中,焦油沉積在電極兩端,則可能引起點火系統失效。生物質氣化氣成分中的大量焦油成分在燃燒過程中會在燃燒室內形成積炭,使得混合氣在火花塞點火前就可能被燃燒室內熾熱的炭粒表面點燃,形成表面點火;同時燃燒室內沉積的積炭過多會增大壓縮比,進而增大爆燃的可能性。而灰分含量太高也會增加運動件之間的磨損,嚴重時會引起拉缸。
2內燃機運行特性分析
測定內燃機不同負荷下的排氣溫度、最大爆發壓力以及燃料消耗率;采用煙度計與氣體分析儀測定尾氣排放中的煙度、NOx、CO、HC。
2.1內燃機的排氣溫度、最大爆發壓力以及有效熱效率特性
生物質氣化氣熱值低,燃燒速度慢,使得單位循環做功指標相對較低,因而選用大缸徑、長行程、大排量、轉速較低的8300作為原型機進行改造[12]。由于生物質氣化氣中含有大量的焦油,在發動機的進氣過程中焦油會黏附在進氣系統的表面上,因此生物質氣化氣發動機不適合對進氣進行增壓,而應選用自然吸氣方式[13]。將原柴油機去除高壓供油系統,進氣管處安裝文丘里管混合器;將燃燒室設計成淺盆形,重新設計活塞,把壓縮比降為9,在原來噴油嘴的位置安裝火花塞;重新設計凸輪軸,優化配氣以及點火正時;同時在總管的兩端安裝安全防爆門等,這些改進使得8300適合燃燒低熱值的生物質氣化氣。
在8300燃氣內燃機600r/min的工況下,對于內燃機的排氣溫度以及動力特性進行了測試,結果見圖2、3。
由圖可看出,隨著發電機組負荷的增加,各缸的排106農業工程學報2008年氣溫度在600℃左右,相對柴油機而言,排氣溫度明顯偏高,原因在于燃燒沖程中混合氣體燃燒不完全,致使后燃嚴重。氣化氣中大量阻燃成分的存在是造成后燃的重要原因,此外由于采用缸外混合氣形成方式,為減少掃氣過程中的混合氣損失,采用30℃A的氣門重疊角,然而氣門重疊角的減小將導致掃氣效果差,缸內的殘余廢氣增多,對于缸內循環的燃燒起抑制作用,進一步加重了后燃現象。加之生物質氣化氣在缸內沒有汽化時的吸熱作用,綜合幾方面的因素,使得燃用生物質氣化氣的內燃機排氣溫度偏高。排氣溫度越高,尾氣所帶走的能量的比重就越大,因而,降低排氣溫度也可以成為提高內燃機熱效率的有效措施。在負荷為500kW左右時,排氣溫度處于低谷,此時通過尾氣帶走的能量相對較少,若不考慮燃燒過程中散熱率的變化,可認為此時段所產生的有效功率相對要高些。
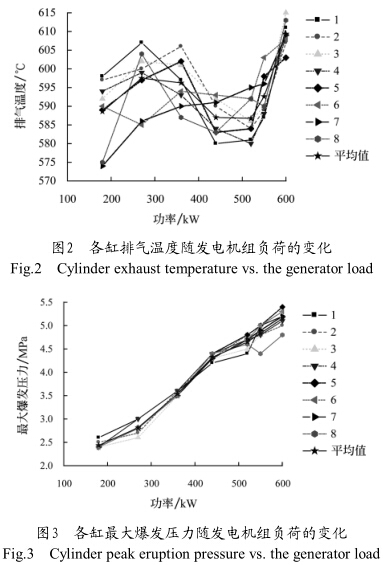
隨著負荷的增加,無論是排氣溫度還是最大爆發壓力都逐漸趨于均勻,各缸的最大爆發壓力逐漸增大。在低負荷時1缸的排氣溫度、最大爆發壓力都要高于其他各缸;但在大負荷時8缸的最大爆發壓力明顯低于其他各缸。進氣總管的壓力較低、氣量不足,是造成各缸排氣溫度、最大爆發壓力不均的重要原因。低負荷時伴隨著較小的進氣量,使得進氣管對于各支管的氣量分配不均,距離進氣管口最近的1缸進氣量相對較多,使得燃燒較為充分;當內燃機處于大負荷時,進氣管的進氣量不足,加之非增壓內燃機的進氣壓力低,使得距離進氣管較遠的8缸,不能夠得到充足的燃氣,燃燒溫度相對較低,最高爆發壓力較低。
通過測定一個時間段中儲氣罐內氣體的消耗量來計算內燃機的氣體消耗率,內燃機所發出的有效功率與消耗的燃氣熱值的比值即為內燃機的有效熱效率。得出內燃機在中等負荷時的有效熱效率最高,為30.4%;全負荷運行時的有效率為29.5%,相對原柴油機明顯偏低。排氣溫度高,最大爆發壓力較低是導致內燃機有效熱效率較低的直接原因。
2.2內燃機的排放特性
對于內燃機煙度的測試采用SF8141A不透光煙度計,對于NOx、CO、HC的排放采用HPC500汽車排氣分析儀,測試結果見圖4。
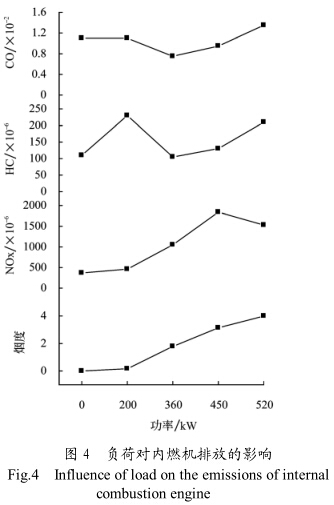
2.2.1煙度
由圖4看出負荷增加使得煙度和每循環進氣量增加,過多的混合氣體進入氣缸,在缸內有限的容積內容易出現局部缺氧,混合氣燃燒不完全,從而使得煙度升高。
衡量內燃機煙度的主要成分是碳煙,因而碳煙的生成率決定了尾氣排放中煙度的高低。導致尾氣中煙度較高的原因有:
1)過量空氣系數的影響
8300燃氣內燃機的過量空氣系數為1.0,采取文丘里管缸外機械預混合方式,理論上能夠使得缸內氣化氣與空氣混合均勻,然而氣化氣的成分不穩定,熱值不斷變化,在實際運行狀況中容易出現局部混合氣過濃或過稀的現象,在缺氧區域利于碳煙的生成。
2)燃燒室形狀的影響
8300燃氣內燃機采用淺盆形燃燒室,由于其不組織渦流,使得燃燒過程中生成的碳煙尚未經過后續燃燒即被排出缸外,增加了碳煙的排量。
2.2.2NOx
無論是燃料的氮還是空氣中的氮都是以無機物的形式存在,分子鍵能高,需要高溫工作環境才能使得氮分子分解成氮原子。
高溫、富氧、氧與氮在高溫中的滯留時間是影響柴油機燃燒過程中NOx生成率大小的三要素[14]。
由圖4看出,中低負荷時,隨負荷的增加,循環進氣量逐漸增多,使得生成NOx的三要素同時加強,必然導致NOx的生成率增加。在高負荷時盡管溫度和高溫滯留時間延長,但NOx生成率下降,原因在于氧濃度的下降制約了氮氧化物的生成速率。
2.2.3CO
對于燃燒生物質氣化氣的內燃機,CO一部分來自混合氣中尚未燃燒的CO;另一部分來自于燃料的不完全燃燒。
圖4表明CO的含量較高,原因在于氣化氣中CO的含量達到15%~18%,因而在缸內燃燒過程中包括縫隙容積在內的部分未燃的CO增加了尾氣中CO的含量。
在低負荷時由于混合氣燃燒不完全,致使其中的部分混合氣中的CO在未參加燃燒的情況下直接排出氣缸;隨著負荷的增大,缸內氣體燃燒趨于完全,CO的生成率降低,中負荷時達到最低值;隨著負荷的增大,CO的生成率呈現增大趨勢,原因在于大負荷時缸內混合氣的進氣量較多,局部缺氧燃燒,導致部分混合氣尚未能完全燃燒就排出氣缸,從而增加了尾氣中的CO含量。
2.2.4HC
碳氫化合物包括混合氣中的未燃或不能完全燃燒的烴類、氣化氣中焦油高溫裂解的產物等。主要是由于缸內混合氣的不完全燃燒造成的。由圖4看出在低負荷時由于缸內氣體的不完全燃燒導致碳氫化合物的生成率增加,中負荷時缸內氣體的燃燒較為完全致使碳氫化合物的含量下降,而在高負荷時過多的混合氣進入氣缸,使得缸內混合氣局部缺氧,尚未完全燃燒即排出缸外,使得碳氫化合物的含量升高。
由上面的試驗分析可以得出以下結論:
1)增大過量空氣系數能有效抑制缸內缺氧的發生,切斷碳煙生成的環境;采用球形、深盆形燃燒室能有效增加缸內的氣體流動,使缸內燃燒成為紊流燃燒,火焰處于運動狀態,從而盡量避免形成局部高溫和局部缺氧,進而抑制碳煙的生成。
2)降低NOx濃度的措施,就是要切斷NOx的滋生環境。增大空燃比,降低壓縮比都能降低NOx的生成率。
3)由于氣化氣中的CO是尾氣中CO的主要來源,使得缸內的混合氣能夠充分的燃燒是降低該部分CO的有效措施。
4)使缸內的混合氣燃燒充分,氣化氣與空氣均勻混合,精確控制空燃比,增加缸內的氣流運動都是能夠降低炭氫化合物的有效措施。
3結論
通過對燃燒生物質氣化氣的內燃機的特性分析發現,氣化氣組分本身的性質是決定內燃機運行特性的主要因素,同時內燃機本身的結構也具有重要影響。8300型內燃機燃用生物質燃氣時的效率最高為30%左右,氣缸內爆發壓力低、排氣溫度高是導致燃氣內燃機效率低下的主要原因;同時燃氣內燃機采用非增壓進氣、燃燒過程中空燃比不穩定、混合氣燃燒不完全也是導致熱效率降低的重要原因。生物質氣化氣的固有成分使得氣缸內混合氣燃燒不完全,以及氫氣對缸內燃燒的不利因素使得內燃機尾氣中的污染物排放較高。
中國的燃氣發動機通過采用增壓、中冷等技術,熱效率能達到35%。國外先進機型通過采用電控混合、稀薄燃燒等閉環控制技術,熱效率已達42%,甚至更高[15]。目前我國對于低熱值燃氣內燃機的研究尚處于起步階段[16],通過以后的不斷探索試驗,期望能夠在原有基礎上不斷提高改進,使得燃氣內燃機在生物質氣化發電中得到更為有效的應用。
[參 考 文 獻]
[1]袁振宏,吳創之,馬隆龍,等.生物質能利用原理與技術[M].北京:化學工業出版社,2005:169-171.
[2]盛建菊. 生物質氣化發電技術的進展[J]. 節能技術, 2007,25(1):67-70.
[3]陰秀麗,周肇秋,馬隆龍,等.生物質氣化發電技術現狀分析[J].現代電力,2007,24(5):48-52.
[4]任永志,崔亨哲,郭 軍,等.生物質氣化發電機組中內燃機的運行特性分析[J]. 可再生能源, 2006, (2): 19-22.
[5]Wu Chuangzhi, Yin Xiuli, Chen Ping, et al. A 5.5MW e biomass demonstration power plant via asification integrated combined cycle[C]. The 3 rd International Green Energy Conference,2007:188-196.
[6]周龍保.內燃機學[M].北京:機械工業出版社,2006:20-25.
[7]劉治中, 許世海, 姚如杰. 液體燃料的性質及應用[M].北京:中國石化出版社,2000:178-204.
[8]項友謙.燃氣熱力工程常用數據手冊[M].北京:中國建筑工業出版社,2000:289-309.
[9]王存磊,朱 磊,袁銀南,等.氫氣在內燃機上的應用及特點[J].拖拉機與農用運輸車,2007,34(3):1-6.
[10]吳創之.生物質燃氣發電技術[J].可再生能源,2003,111(5):58-60.
[11]陳 平.生物質流化床氣化機理與工業應用研究[D].合肥:中國科學技術大學,2006.
[12]高緒偉,李宗立,辛強之.8300 生物質氣體發動機的開發及初步試驗[J].山東內燃機,2002,72(2):72-75.
[13]王令金.大型火花點火生物質氣發電機組的研究開發[D].濟南:山東大學,2006.
[14]何學良,李疏松.內燃機燃燒學[M].北京:機械工業出版社,1990:440-466.
[15]陳宜亮.燃氣發動機的發展動向[J].山東內燃機,2004,82(4):4-7.
[16]孟凡生,陰秀麗,蔡建渝,等.我國低熱值燃氣內燃機的研究現狀[J].內燃機,2007,128(3):46-49. |